What Does It Cost to Manufacture Car Refrigerators
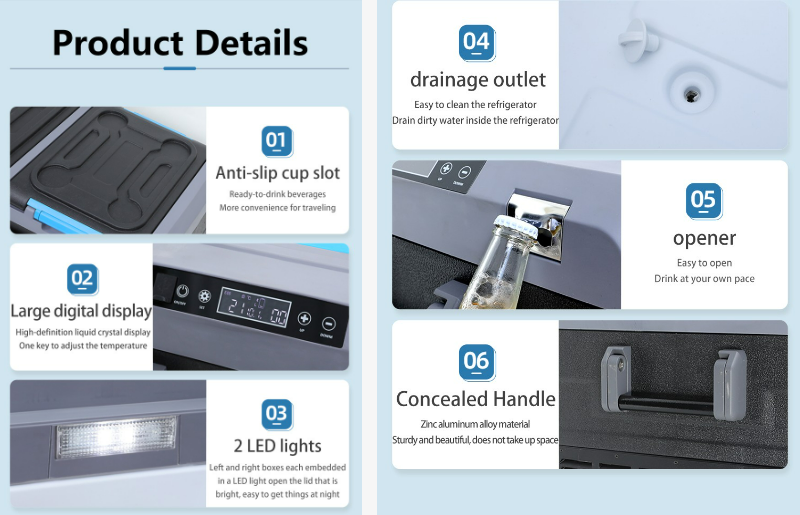
The cost to manufacture car refrigerators varies widely, typically ranging from
50to300 per unit. This variation depends on factors such as the size of the refrigerator, the features it offers, and the scale of production. Smaller units with basic functionality cost less, while larger models with advanced technology require higher investments. Understanding these costs helps you grasp how manufacturers balance affordability with quality. The car refrigerator manufacturing cost also reflects the materials and labor involved, making it a key factor in determining the final price.
Key Takeaways
- Manufacturing costs for car refrigerators typically range from
50to300, influenced by size, features, and production scale.
- Larger refrigerators require more materials, increasing production costs, while compact models are generally more affordable.
- Advanced features like digital controls and smart connectivity enhance convenience but also raise manufacturing expenses.
- The choice of materials impacts both the durability and cost of car refrigerators; high-quality materials lead to better performance but higher prices.
- Labor costs vary based on skill level and production scale; automation can reduce expenses but requires initial investment.
- Overhead costs, including packaging and shipping, significantly contribute to the final price of car refrigerators.
- Understanding these cost factors helps consumers make informed decisions when purchasing car refrigerators.
Key Factors Influencing Car Refrigerator Manufacturing Cost
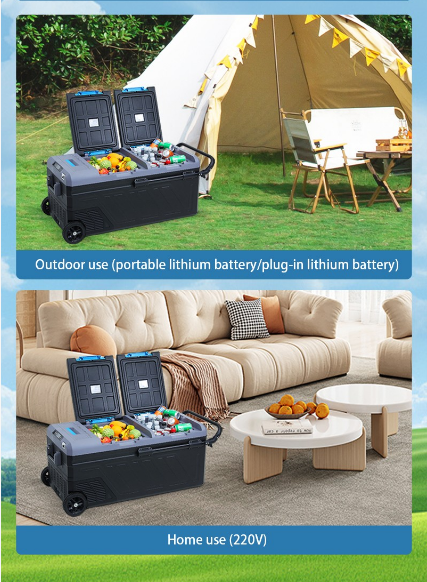
Size and Capacity
The size and capacity of a car refrigerator play a significant role in determining its manufacturing cost. Larger refrigerators require more materials, which increases production expenses. A compact unit designed for small vehicles uses fewer resources, making it less expensive to produce. Manufacturers must carefully balance size and capacity to meet consumer needs while keeping costs manageable. You should consider how the size of a refrigerator impacts not only its price but also its functionality and energy efficiency.
Features and Technology
Advanced features and modern technology significantly influence the car refrigerator manufacturing cost. Refrigerators with digital temperature controls, energy-saving modes, or smart connectivity require sophisticated components. These features enhance user convenience but add to production expenses. Basic models with fewer features are more affordable to manufacture. When evaluating a car refrigerator, you should think about whether the added features justify the higher cost.
Materials and Components
The choice of materials and components directly affects the cost of manufacturing car refrigerators. High-quality materials, such as stainless steel or durable plastics, increase durability but raise production costs. Cheaper materials reduce expenses but may compromise the product’s lifespan. Components like compressors, insulation, and cooling systems also vary in price based on their quality and efficiency. You should understand that the materials used in a refrigerator impact both its cost and performance.
Labor and Production Scale
Labor and production scale significantly impact the cost of manufacturing car refrigerators. The number of workers involved in the production process directly influences expenses. Skilled labor ensures high-quality assembly, but it comes at a higher cost. On the other hand, unskilled labor may reduce expenses but could compromise the product’s quality.
The scale of production also plays a crucial role. Large-scale manufacturing often reduces costs due to economies of scale. When manufacturers produce car refrigerators in bulk, they can negotiate better prices for raw materials and components. This approach lowers the overall production cost per unit. In contrast, small-scale production tends to increase costs because fixed expenses, like machinery and factory maintenance, are spread across fewer units.
Automation in production lines can further optimize labor costs. Automated systems reduce the need for manual labor, speeding up the manufacturing process and minimizing errors. However, implementing automation requires a significant initial investment, which may affect the car refrigerator manufacturing cost in the short term.
Understanding how labor and production scale influence costs helps you appreciate the balance manufacturers must strike between quality, efficiency, and affordability.
Detailed Breakdown of Car Refrigerator Manufacturing Cost
Raw Materials
Raw materials form the foundation of any car refrigerator. These include metals, plastics, insulation, and electronic components. High-quality materials like stainless steel or durable polymers ensure longevity and performance. However, they also increase the car refrigerator manufacturing cost. Cheaper alternatives may reduce expenses but often compromise durability and efficiency.
The type of cooling system used also impacts material costs. Compressors, thermoelectric modules, and refrigerants vary in price. For example, a compressor-based system requires more expensive components than a thermoelectric one. You should note that manufacturers often balance material quality with cost to meet market demands.
Labor Costs
Labor costs directly influence the final expense of manufacturing car refrigerators. Skilled workers assemble components, test functionality, and ensure quality control. Their expertise guarantees a reliable product but raises production costs. In regions with higher wages, labor expenses can significantly increase the overall cost.
Automation helps reduce labor costs by streamlining production. Machines handle repetitive tasks, allowing manufacturers to focus on quality and efficiency. However, implementing automation requires an upfront investment. You might find that manufacturers in competitive markets rely on a mix of skilled labor and automation to optimize costs.
Overhead and Indirect Costs
Overhead and indirect costs cover expenses beyond raw materials and labor. These include factory maintenance, energy consumption, equipment depreciation, and administrative costs. For instance, maintaining a temperature-controlled environment for assembly lines adds to the car refrigerator manufacturing cost.
Packaging and shipping also fall under this category. Protective packaging ensures the product reaches customers in perfect condition. Shipping costs depend on the destination and method of transport. You should understand that these indirect expenses contribute to the final price of a car refrigerator.
Packaging and Shipping
Packaging and shipping play a crucial role in the overall cost of manufacturing car refrigerators. Manufacturers must ensure that the product reaches customers in perfect condition, which requires careful planning and execution.
Packaging involves selecting materials that protect the refrigerator during transit. Sturdy boxes, foam inserts, and bubble wrap are common choices. These materials prevent damage from impacts or vibrations. High-quality packaging materials increase costs but reduce the risk of returns due to damaged goods. You should know that manufacturers often balance durability with cost-effectiveness when choosing packaging solutions.
Shipping costs depend on factors like distance, weight, and transportation method. Air freight offers faster delivery but comes at a higher price. Sea or ground shipping is more affordable but takes longer. Bulk shipping reduces costs per unit, making it a preferred option for large-scale manufacturers. You might notice that smaller companies often face higher shipping expenses due to limited volume.
Customs duties and taxes also add to shipping costs, especially for international deliveries. Manufacturers must comply with regulations in different countries, which can increase expenses. Efficient logistics management helps minimize these costs. You should understand that streamlined shipping processes contribute to competitive pricing for car refrigerators.
Sustainable packaging and shipping practices are gaining popularity. Eco-friendly materials and carbon-neutral shipping options appeal to environmentally conscious consumers. These practices may slightly increase costs but enhance brand reputation. You might find that many manufacturers are adopting these methods to meet market demands while maintaining profitability.
Overview of the Car Refrigerator Manufacturing Process
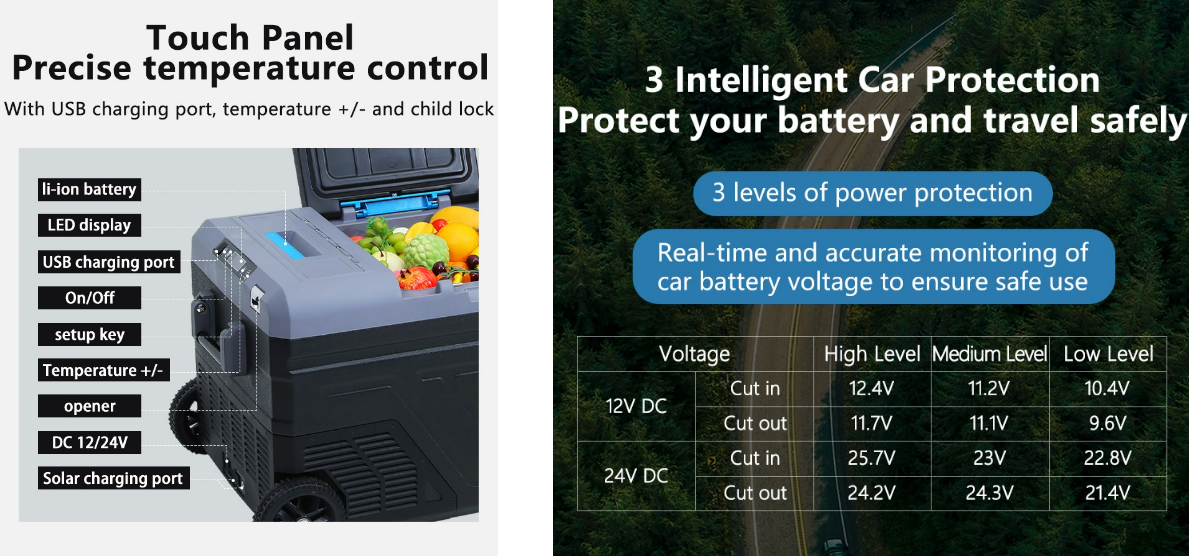
Design and Prototyping
The manufacturing process begins with design and prototyping. Engineers create detailed blueprints that outline the refrigerator’s dimensions, features, and functionality. These designs focus on balancing efficiency, durability, and cost-effectiveness. You will notice that manufacturers often use computer-aided design (CAD) software to refine these plans and ensure precision.
Prototyping follows the design phase. Manufacturers build a working model to test the refrigerator’s performance and identify potential flaws. This step allows them to make adjustments before mass production begins. You should understand that prototyping ensures the final product meets quality standards and customer expectations.
Component Sourcing and Assembly
After finalizing the design, manufacturers source the necessary components. These include compressors, cooling systems, insulation materials, and electronic controls. Reliable suppliers provide high-quality parts that enhance the refrigerator’s performance. You might find that sourcing components locally reduces costs and speeds up production.
The assembly process combines these components into a functional unit. Workers or automated systems follow precise instructions to ensure consistency. Each part fits together seamlessly to create a durable and efficient product. Manufacturers often conduct inspections during assembly to maintain quality. You should know that this step directly impacts the car refrigerator manufacturing cost and the product’s reliability.
Final Testing and Packaging
Once assembly is complete, manufacturers test the refrigerators to verify their performance. They check cooling efficiency, energy consumption, and durability under various conditions. These tests ensure the product meets safety and quality standards. You might notice that rigorous testing reduces the risk of defects and enhances customer satisfaction.
Packaging comes next. Manufacturers use protective materials to shield the refrigerator during transit. Sturdy boxes, foam padding, and secure seals prevent damage. This step ensures the product reaches you in perfect condition. Efficient packaging also minimizes waste and aligns with sustainable practices.
The manufacturing process concludes with shipping. Manufacturers coordinate logistics to deliver the refrigerators to retailers or customers. You should understand that every step in this process contributes to the final product’s quality and price.
Manufacturing car refrigerators requires balancing multiple factors to manage costs effectively. The car refrigerator manufacturing cost typically ranges from
50to300 per unit, depending on size, features, and production scale. Materials, labor, and overhead expenses form the core of these costs. The manufacturing process, from design to final testing, ensures quality and efficiency. Advancements in energy efficiency and smart technology continue to influence designs and pricing. Understanding these elements helps you make informed decisions when evaluating car refrigerators.
FAQ
What is the average cost to manufacture a car refrigerator?
The average cost to manufacture a car refrigerator ranges from
50to300 per unit. This cost depends on factors like size, features, materials, and production scale. Smaller models with basic features cost less, while larger units with advanced technology require higher investments.
Why do advanced features increase manufacturing costs?
Advanced features, such as digital temperature controls or smart connectivity, require sophisticated components. These components are more expensive to produce and assemble. Adding these features enhances functionality but increases the overall manufacturing cost.
How does the size of a car refrigerator affect its cost?
Larger refrigerators require more materials and components, which raises production costs. Compact models use fewer resources, making them more affordable to manufacture. The size also impacts energy efficiency and functionality, which manufacturers consider during production.
What materials are commonly used in car refrigerators?
Manufacturers use materials like stainless steel, durable plastics, insulation foam, and electronic components. High-quality materials improve durability and performance but increase costs. Cheaper alternatives reduce expenses but may compromise the product’s lifespan.
How does labor influence the cost of manufacturing?
Skilled labor ensures precise assembly and quality control, which raises production costs. Automation reduces labor expenses by streamlining repetitive tasks. However, implementing automation requires an initial investment, which can temporarily increase costs.
What role does packaging play in the overall cost?
Packaging protects the refrigerator during transit. Manufacturers use materials like sturdy boxes, foam inserts, and bubble wrap to prevent damage. High-quality packaging increases costs but reduces the risk of returns due to damaged goods.
Are there ways manufacturers reduce shipping costs?
Manufacturers often use bulk shipping to lower costs per unit. They also optimize logistics to minimize expenses. Choosing affordable transportation methods, like sea or ground shipping, helps reduce shipping costs compared to air freight.
How do manufacturers ensure the quality of car refrigerators?
Manufacturers conduct rigorous testing after assembly. They check cooling efficiency, energy consumption, and durability under various conditions. These tests ensure the product meets safety and quality standards before reaching customers.
What is the impact of sustainable practices on manufacturing costs?
Sustainable practices, like using eco-friendly materials and carbon-neutral shipping, slightly increase costs. However, these practices appeal to environmentally conscious consumers and enhance brand reputation. Many manufacturers adopt these methods to meet market demands.
How does production scale affect manufacturing costs?
Large-scale production reduces costs due to economies of scale. Manufacturers producing in bulk negotiate better prices for raw materials and components. Small-scale production increases costs because fixed expenses are spread across fewer units.
Post time: Dec-10-2024