Compressor Fridge Hacks to Build Silent Air Units
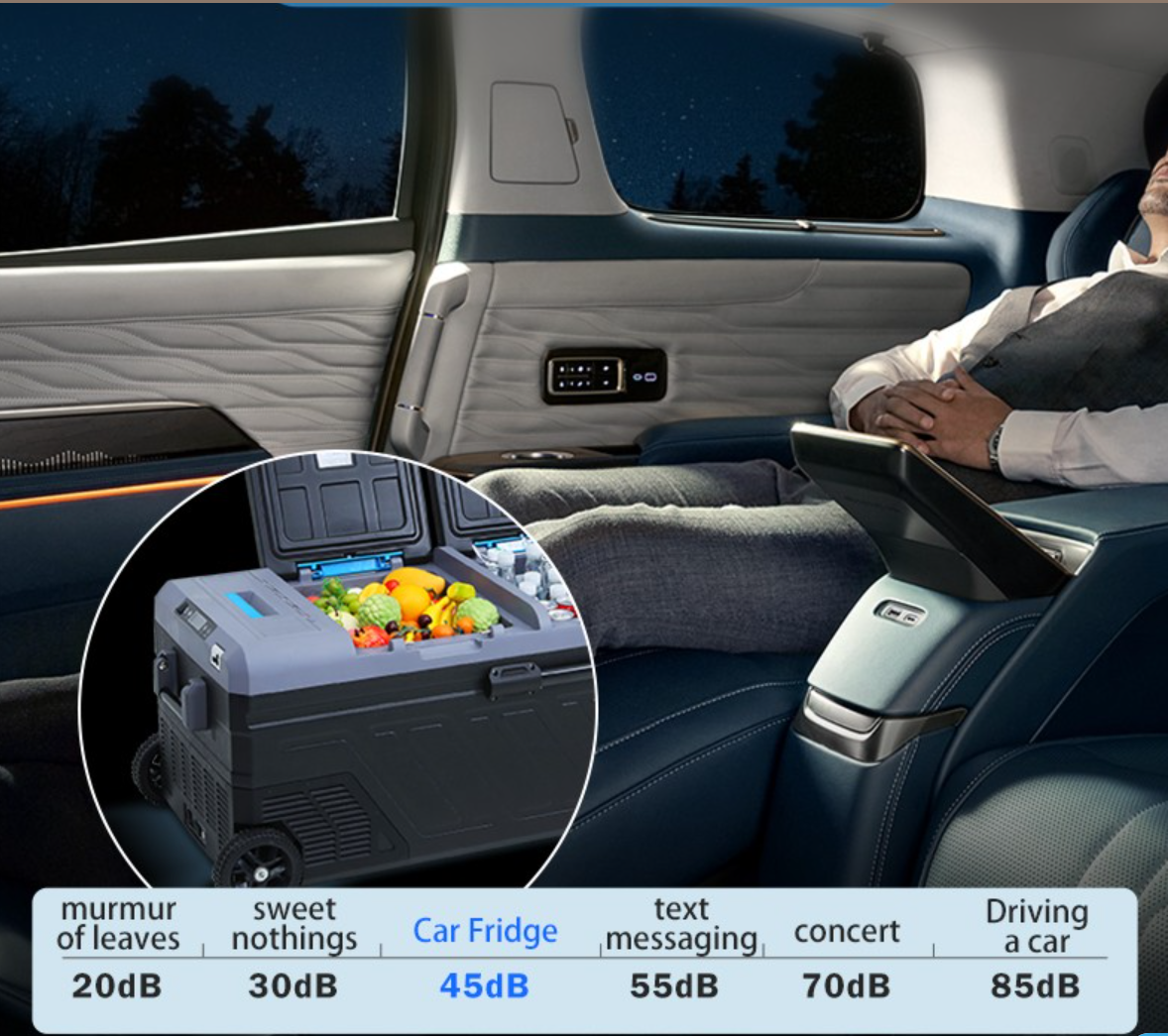
Key Takeaways
- Transforming a compressor fridge into a silent air compressor is a rewarding DIY project that combines creativity and technical skills.
- Gather essential tools like screwdrivers, wrenches, and a pipe cutter to ensure a smooth modification process.
- Prioritize safety by wearing protective gear and handling refrigerants responsibly to avoid health risks.
- Regular maintenance, including cleaning air filters and checking for leaks, is crucial for the longevity and efficiency of your modified air compressor.
- The modified air compressor operates quietly, making it ideal for use in noise-sensitive environments like home workshops.
- Repurposing a fridge compressor is a cost-effective solution that allows for customization and versatility in various applications.
- Testing the system for leaks and ensuring proper functionality is essential for creating a reliable and efficient silent air unit.
Tools and Materials for Compressor Fridge Modification
When modifying a compressor fridge into a silent air unit, having the right tools and materials is essential. I always ensure that my workspace is organized before starting any project. This preparation saves time and prevents unnecessary interruptions.
Essential Tools
To begin, I gather a set of basic tools. These tools make the disassembly and assembly process smooth and efficient.
-
Screwdrivers and wrenches
Screwdrivers and wrenches are indispensable for removing screws and bolts from the fridge. I use them to detach the compressor and other components securely.
-
Pipe cutter or hacksaw
A pipe cutter or hacksaw is necessary for cutting pipes and fittings to the required size. I prefer a pipe cutter for its precision, but a hacksaw works well for tougher materials.
-
Drill and drill bits
Drills come in handy when creating holes for mounting or attaching components. I select drill bits based on the material I’m working with to ensure clean and accurate holes.
Required Materials
The materials I choose determine the functionality and durability of the modified air compressor. Each component plays a critical role in the system.
-
Fridge compressor
The fridge compressor is the heart of this project. I carefully remove it from the compressor fridge, ensuring it remains intact for optimal performance.
-
Air tank
An air tank stores compressed air. I select a tank with the appropriate capacity to match the compressor’s output.
-
Hoses and fittings
Hoses and fittings connect the compressor to the air tank and other components. I ensure they are compatible and leak-proof.
-
Pressure gauge and safety valve
A pressure gauge monitors the air pressure, while a safety valve prevents over-pressurization. These components are vital for safe operation.
-
Teflon tape and clamps
Teflon tape seals threaded connections, and clamps secure hoses in place. I use these to prevent air leaks and maintain system integrity.
-
Air/oil separator with return system
The air/oil separator removes oil from the compressed air. I include a return system to recycle the oil back into the compressor, ensuring proper lubrication.
Safety Gear
Safety is my top priority during any DIY project. I always equip myself with the necessary protective gear.
-
Gloves
Gloves protect my hands from sharp edges and harmful substances. I choose durable gloves that provide a good grip.
-
Safety goggles
Safety goggles shield my eyes from debris and refrigerant splashes. I never skip this step to avoid potential injuries.
-
Mask for handling refrigerants
Refrigerants can be hazardous if inhaled. I wear a mask to protect my respiratory system when dealing with these substances.
By using the right tools, materials, and safety gear, I ensure the modification process is efficient and safe. This preparation lays the foundation for a successful compressor fridge transformation.
Step-by-Step Guide to Modifying a Compressor Fridge
Preparing the Fridge Compressor
I start by carefully removing the compressor from the fridge. This step requires precision and patience. I use screwdrivers and wrenches to detach the compressor without damaging any components. Handling the compressor with care ensures it remains functional for the modification process.
Once removed, I drain any remaining refrigerant from the compressor. Refrigerants can be hazardous, so I always wear a mask and ensure proper ventilation in my workspace. After draining, I clean the compressor thoroughly. Removing dirt and residue improves its performance and longevity. A clean compressor sets the foundation for a reliable silent air unit.
Connecting the Air Tank
Next, I connect the compressor to the air tank. I select fittings that match the size of the compressor’s outlet and the air tank’s inlet. Using the correct fittings prevents air leaks and ensures a secure connection. I attach the compressor to the air tank by tightening the fittings with a wrench.
To reinforce the connection, I apply Teflon tape to the threaded areas. This tape creates an airtight seal, reducing the risk of leaks. I also use clamps to secure the hoses firmly in place. These steps guarantee a stable and efficient connection between the compressor and the air tank.
Adding a Pressure Gauge and Safety Valve
Installing a pressure gauge comes next. I attach the gauge to the air tank to monitor the air pressure during operation. This tool helps me maintain the desired pressure level and avoid over-pressurization. I ensure the gauge is positioned where it is easy to read.
I then add a safety valve to the system. This valve acts as a fail-safe mechanism, releasing excess pressure if it exceeds the recommended limit. I test the valve to confirm it functions correctly. Including a safety valve enhances the overall safety of the modified compressor fridge.
By following these steps, I transform a compressor fridge into a silent air unit. Each stage of the process requires attention to detail and adherence to safety protocols. The result is a functional and efficient air compressor ready for various applications.
Testing the System
Check all connections for leaks.
I begin by inspecting every connection in the system. I focus on the joints where hoses, fittings, and components meet. Leaks can compromise the efficiency of the air unit, so I take this step seriously. To check for leaks, I use a simple soap and water solution. I apply the solution to each connection and watch for bubbles. Bubbles indicate escaping air, which signals a leak. When I find a leak, I tighten the connection or replace the faulty component. This method ensures that the system remains airtight and ready for operation.
Power on the compressor and test its functionality.
After confirming that all connections are secure, I power on the compressor. I connect it to a reliable power source and switch it on. I listen closely for any unusual sounds, as these can indicate internal issues. A properly functioning compressor fridge should operate quietly and smoothly. I monitor the pressure gauge to ensure the system builds pressure efficiently. If the pressure rises steadily and reaches the desired level, I know the system is working correctly. I also test the safety valve by releasing excess pressure. This step confirms that the valve functions as intended, adding an extra layer of safety to the system.
Testing the system is a critical phase in the modification process. It verifies the integrity of the connections and the performance of the compressor fridge. By addressing leaks and ensuring proper functionality, I create a reliable and efficient silent air unit.
Safety Tips for Compressor Fridge Modifications
Safety remains my top priority when modifying a compressor fridge. I take every precaution to ensure the process is secure and efficient. Following these safety tips helps me avoid accidents and ensures the longevity of the modified air unit.
Handling Refrigerants
Refrigerants require careful handling due to their hazardous nature. I always work in a well-ventilated area when removing refrigerants from the compressor fridge. Proper ventilation prevents the buildup of harmful fumes, which could pose health risks. I also wear a mask to protect my respiratory system during this step.
Disposing of refrigerants responsibly is equally important. I follow local regulations to ensure safe disposal. Many areas have designated facilities for refrigerant recycling or disposal. I contact these facilities to handle the refrigerants properly. This practice not only protects the environment but also complies with legal requirements.
Electrical Safety
Electrical safety is critical when working with any appliance. Before removing the compressor, I disconnect the fridge from its power source. This step eliminates the risk of electric shock. I double-check that the power cord is unplugged before proceeding.
Using insulated tools adds another layer of protection. I select tools specifically designed for electrical work. These tools prevent accidental contact with live wires, reducing the risk of injury. By taking these precautions, I ensure a safe working environment throughout the modification process.
Pressure Safety
Pressure safety is essential when dealing with compressed air systems. I never exceed the recommended pressure limits of the air tank. Over-pressurization can lead to dangerous situations, including tank failure. I rely on the pressure gauge to monitor the system and maintain safe operating levels.
Regular inspection of the safety valve is another crucial step. I test the valve periodically to confirm it functions correctly. A well-maintained safety valve releases excess pressure, preventing potential accidents. These measures help me operate the modified compressor fridge with confidence and peace of mind.
By adhering to these safety tips, I create a secure and efficient workspace. Each precaution minimizes risks and ensures the success of the project. Safety remains the cornerstone of every modification I undertake.
Maintenance and Troubleshooting for Silent Air Compressors
Proper maintenance ensures the longevity and efficiency of a silent air compressor. I follow a consistent routine to keep my compressor fridge modification in top condition. Regular checks and timely troubleshooting prevent potential issues and maintain optimal performance.
Regular Maintenance
Clean the air filter periodically.
The air filter plays a crucial role in maintaining clean airflow within the system. I inspect the filter regularly and remove any accumulated dust or debris. A clogged filter reduces efficiency and increases strain on the compressor. I clean it using compressed air or replace it if necessary. This simple step keeps the system running smoothly.
Check for leaks in hoses and fittings.
Leaks compromise the performance of the air compressor. I examine all hoses and fittings for signs of wear or damage. Loose connections often cause air loss, so I tighten them as needed. For damaged hoses, I replace them immediately. Regular inspections help me identify and resolve leaks before they escalate into bigger problems.
Troubleshooting Common Issues
Compressor not starting: Check power supply and connections.
When the compressor fails to start, I first verify the power supply. I ensure the plug is securely connected to a functioning outlet. If the issue persists, I inspect the wiring and connections for any visible damage. Faulty connections often disrupt power flow. I use a multimeter to test the electrical components and replace any defective parts.
Low pressure: Inspect for leaks or blockages in the system.
Low pressure indicates a problem within the system. I begin by checking for leaks in the hoses, fittings, or air tank. Using a soap and water solution, I identify leaks by observing bubbles at the connection points. Blockages in the system also reduce pressure. I disassemble the affected components and clear any obstructions. These steps restore the system’s pressure and efficiency.
By following these maintenance practices and troubleshooting techniques, I ensure my compressor fridge modification operates reliably. Consistent care minimizes downtime and extends the lifespan of the unit.
Benefits of a Compressor Fridge Silent Air Unit
Noise Reduction
I find the noise reduction of a compressor fridge silent air unit remarkable. The modified system operates with minimal sound, making it ideal for indoor use. I often use mine in noise-sensitive environments like home workshops or shared spaces. The quiet operation ensures I can work without disturbing others. This feature proves especially useful during late hours or in areas where maintaining a peaceful atmosphere is essential.
Cost-Effective DIY Solution
Repurposing a fridge compressor offers a cost-effective alternative to purchasing a new air compressor. I save money by utilizing components from an old fridge, which reduces the need for expensive equipment. The DIY approach also allows me to customize the unit according to my needs. I enjoy the satisfaction of creating a functional and efficient air compressor without overspending. This project demonstrates how resourcefulness can lead to significant savings while achieving professional-grade results.
Versatility
The versatility of a compressor fridge silent air unit impresses me. I use mine for various applications, including inflating tires, airbrushing, and powering pneumatic tools. The system adapts to different tasks with ease, making it a valuable addition to my toolkit. Its compact design and portability enhance its usability in diverse settings. Whether I’m working in my garage or outdoors, the unit performs reliably. This flexibility ensures I get the most out of my DIY project.
Transforming a compressor fridge into a silent air compressor offers a rewarding and practical DIY experience. I find this project not only cost-effective but also highly versatile for various applications. By following the outlined steps and prioritizing safety, you can build a reliable and efficient air unit. This project allows you to repurpose materials creatively while saving money. I encourage you to take on this challenge and enjoy the satisfaction of crafting a custom-built silent air compressor that meets your specific needs.
FAQ
What is the purpose of modifying a fridge compressor into a silent air unit?
I modify a fridge compressor to create a quiet and efficient air compressor. This DIY project repurposes old components, reduces noise levels, and provides a cost-effective solution for various applications like inflating tires or powering tools.
Can I use any fridge compressor for this modification?
Yes, most fridge compressors work for this project. I recommend using a compressor from a functional fridge or freezer. Ensure the compressor is in good condition to achieve optimal performance after modification.
How do I ensure safety when handling refrigerants?
I always prioritize safety when dealing with refrigerants. Work in a well-ventilated area to avoid harmful fumes. Wear a mask to protect your respiratory system. Dispose of refrigerants responsibly by following local regulations or contacting designated facilities.
What tools are essential for this project?
I rely on basic tools like screwdrivers, wrenches, a pipe cutter or hacksaw, and a drill with drill bits. These tools help with disassembly, cutting, and mounting components during the modification process.
How do I prevent leaks in the system?
To prevent leaks, I use Teflon tape on threaded connections and secure hoses with clamps. I also test all connections with a soap and water solution. If bubbles appear, I tighten the fittings or replace faulty components.
What are the benefits of dual cooling zones in a refrigerator?
Dual cooling zones allow me to store different types of food at separate temperatures. This feature provides flexibility for refrigeration and freezing needs. It ensures optimal storage conditions for various items.
Can I customize the modified air compressor?
Yes, customization is possible. I often add features like Bluetooth speakers, lithium batteries with power management, or retractable handles and wheels. These additions enhance functionality and convenience.
How do I maintain the modified air compressor?
Regular maintenance keeps the system efficient. I clean the air filter periodically and inspect hoses and fittings for leaks. Addressing minor issues promptly prevents larger problems and extends the unit’s lifespan.
Is the modified air compressor suitable for outdoor use?
Yes, it works well outdoors. The anti-shock and anti-tilt design ensures stability on uneven surfaces. Its compact size and portability make it ideal for outdoor activities and remote tasks.
What makes this project cost-effective?
Repurposing a fridge compressor saves money compared to buying a new air compressor. I use readily available materials and tools, which reduces expenses. The DIY approach also eliminates labor costs, making it an affordable solution.
Post time: Dec-05-2024